The Ultimate Guide to Low Pressure Casting
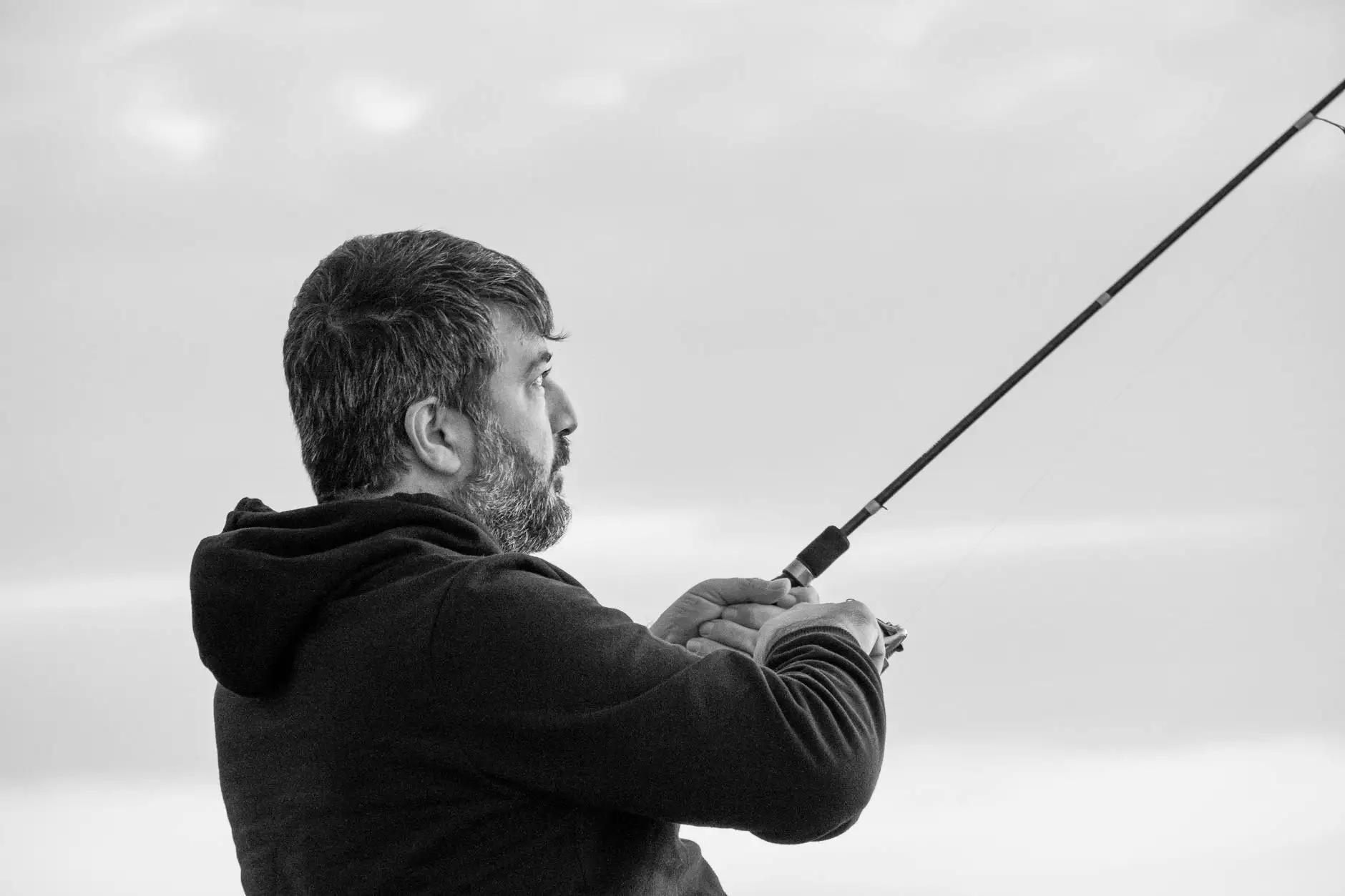
Low pressure casting is an innovative manufacturing technique that has gained popularity across various industries, including art supplies, product design, and 3D printing. This method not only enhances the quality of the products but also revolutionizes the way prototypes and finished goods are created. In this comprehensive guide, we will explore the ins and outs of low pressure casting, its benefits, applications, and how it stands out in the competitive landscape of modern manufacturing.
What is Low Pressure Casting?
Low pressure casting involves the process of pouring liquid material into a mold under controlled atmospheric pressure. Unlike traditional casting methods, where gravity takes the role of filling the mold, low pressure casting utilizes a compressed air system to push the liquid into the mold cavity. This technique results in fewer defects, improved surface quality, and more precise dimensions.
How Does Low Pressure Casting Work?
The process can be broken down into several key steps:
- Mold Preparation: A high-quality mold is created, typically from a durable material like aluminum, which can withstand the pressure of the casting process.
- Material Selection: The liquid metal or resin is chosen based on the desired properties of the final product.
- Application of Low Pressure: Compressed air is introduced to the casting chamber, creating a low-pressure environment that forces the liquid material into the mold.
- Curing: Once filled, the material is allowed to cure and solidify, taking on the shape of the mold.
- Demolding: After curing, the completed piece is carefully removed from the mold.
The Advantages of Low Pressure Casting
Embracing low pressure casting comes with numerous benefits, making it an attractive option for designers and manufacturers alike. Here are some of the most significant advantages:
1. Enhanced Quality and Precision
Low pressure casting allows for excellent surface finish and dimensional accuracy. The controlled environment reduces the likelihood of defects such as air bubbles and impurities, leading to superior quality castings.
2. Greater Material Efficiency
This casting technique minimizes waste by ensuring that the materials are used effectively. The controlled pressure allows for better filling of the mold, which significantly reduces the amount of surplus material required.
3. Versatility in Applications
Low pressure casting can be used with various materials, including metals, plastics, and resins. This versatility makes it suitable for a wide range of sectors, from creating intricate art pieces to functional mechanical components.
4. Faster Production Times
With quicker mold filling and shorter curing times, low pressure casting can significantly expedite the manufacturing process. This efficiency allows businesses to meet tighter deadlines and respond more effectively to market demands.
Applications of Low Pressure Casting
The range of applications for low pressure casting is vast and diverse. Here are some of the key areas where this casting technique shines:
1. Art Supplies
In the realm of art supplies, low pressure casting is increasingly being used to create high-quality molds for sculptures, custom art pieces, and other creative projects. Artists appreciate the ability to achieve intricate details and durable finishes, allowing their visions to come to life in stunning ways.
2. Product Design
Product designers leverage low pressure casting to prototype new products quickly. The ability to produce accurate and detailed prototypes means that designers can conduct thorough testing and iterations, leading to higher-quality end products. This feature is particularly beneficial in industries such as consumer electronics, automotive, and aerospace design.
3. 3D Printing
Integrating low pressure casting with 3D printing technology enhances the overall manufacturing process. Designers can 3D print parts that serve as lost wax patterns or produce molds for casting, combining the best of both worlds to create unique and custom products.
Choosing the Right Materials for Low Pressure Casting
The success of any low pressure casting project significantly depends on the choice of materials. Here are some options available across different sectors:
1. Metals
Common metals used in low pressure casting include:
- Aluminum: Lightweight, corrosion-resistant, and excellent mechanical properties make aluminum a popular choice.
- Magnesium: Offers high strength-to-weight ratios, commonly utilized in automotive and aerospace industries.
- Brass and Bronze: These alloys create beautiful and durable castings ideal for artistic applications.
2. Resins
Resins utilized in low pressure casting often offer unique aesthetics and properties:
- Epoxy Resins: Known for their strong bonding capabilities and resistance to environmental factors.
- Polyurethane Resins: Flexible and impact-resistant, suitable for a wide range of applications.
Tips for Successful Low Pressure Casting
To achieve the best results with your low pressure casting projects, consider these essential tips:
- Invest in Quality Molds: High-quality molds ensure better final outcomes. Choose durable materials and precise manufacturing techniques.
- Control Environmental Factors: Keep temperature and humidity levels stable to avoid any adverse effects on the casting process.
- Conduct Thorough Testing: Always perform trial runs to understand the material behavior and make necessary adjustments to your technique.
The Future of Low Pressure Casting
As industries continue to evolve and demand for innovative solutions rises, the future of low pressure casting looks promising. The integration of smart technologies, enhanced materials, and automation will likely lead to even greater efficiencies and improved product quality. Companies like arti90.com are poised to harness these advancements, driving forward the fields of art supplies, product design, and 3D printing while setting new standards for excellence.
Conclusion
In summary, low pressure casting stands as a transformative technique that offers numerous benefits across various sectors, particularly in art supplies, product design, and 3D printing. By understanding its processes, advantages, and applications, businesses can harness its power to create exceptional products effectively and efficiently. Embrace the future of manufacturing with low pressure casting and elevate your creations to new heights.